Choosing the Right Table Saw Blade
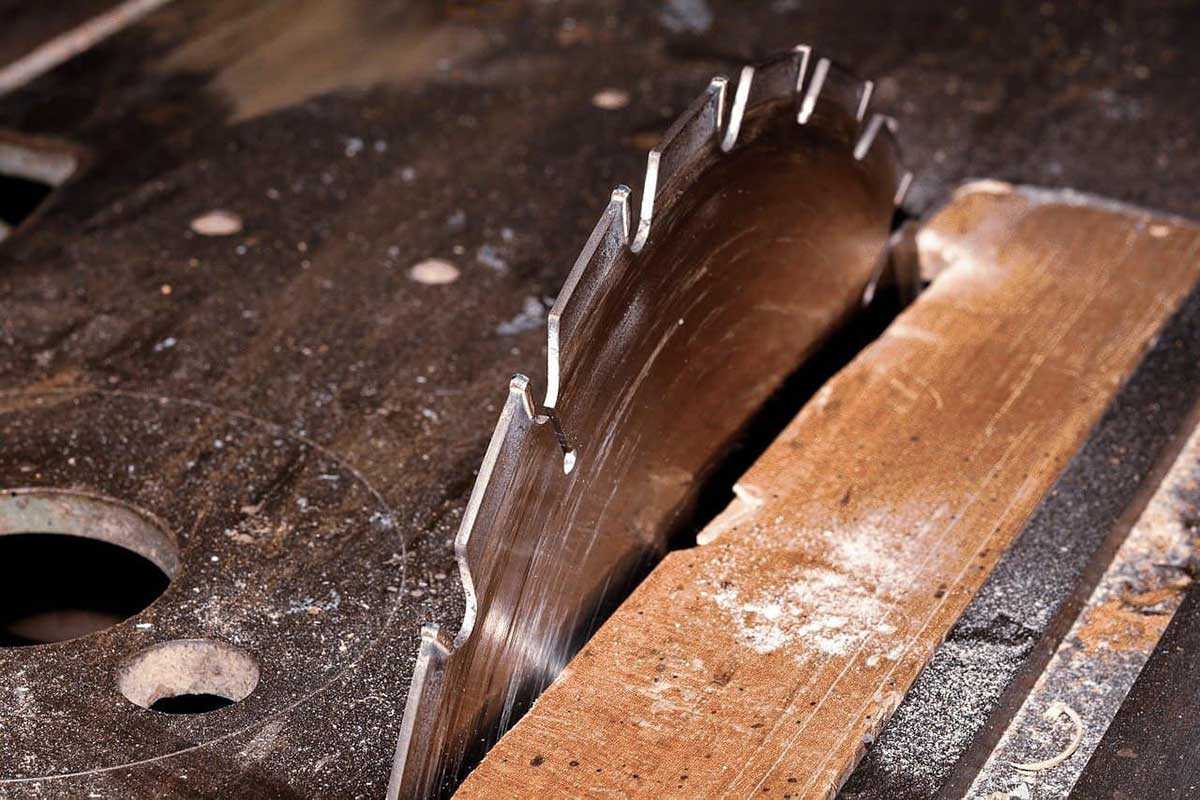
From gullet to kerf, this guide will demystify the terms you need to know and teach you how to choose the right table saw blade for your next project.
Table saw blades seem pretty simple at heart—round pieces of steel with teeth, right? But if you’re a DIY-ing homeowner like me, the array of terminology you run into can seem bewildering. In this guide, I’ll walk you through all the terms you’ll see when choosing the best table saw blade for your project. And I’ll explain which ones actually matter. Picking the right blade will let you execute your project safely and efficiently.
Related: The 9 Best Table Saw Blades
If you haven’t yet bought a saw, check out our companion guide on how to choose the right table saw. And brush up on our guidelines for safe operation of your table saw and blade.
Characteristics of Table Saw Blades
Before deciding which blade to buy, it’s good to know the factors that set different table saw blade types apart.
Blade Tooth Configuration
The shape of the teeth makes a huge impact on how a saw blade will cut through different materials. Some blades have a single type of tooth, while others have more than one. The following four sections will cover most of the blades you’re likely to come across for typical projects.
Flat-top (FT)
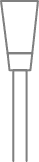
Also referred to as flat-top grind (FTG), these teeth run flat across the width of the saw. They chew chunks out of the wood rather than slicing through it. This makes them best suited for ripping wood lengthwise with the grain. Ripping with the grain takes much less effort than cutting across the wood fibers.
The force with which they tear through material can cause problems. It can lead to significant chipping in materials like melamine and laminates. And in material like plywood, you can experience a high degree of tear-out.
Alternate Top Bevel (ATB)
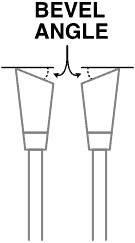
The cutting edges of these teeth angle up or down rather than straight across. The direction of these bevels alternates between teeth. The bevels act like a knife slicing through the wood rather than chewing out chunks. This slicing behavior results in cleaner cuts across the grain.
The bevel angle may be shallow or steep, depending on the material the blade is meant for. Typical bevel angles are between 10 and 20 degrees, where 0 degrees would be flat across as on an FT blade. A variant called a high-angle alternate top bevel (Hi-ATB) blade has steeper angles. At 25 to 40 degrees, these teeth excel at cutting hardwood plywood or melamine.
Because beveled teeth have less “meat” to them than FT teeth, they are also less durable and will wear out sooner.
Alternate Top Bevel/Raker (ATBR) or Combination
Combination blades have both ATB and FT teeth so they can make both rip-cuts and cross-cuts. The configuration usually consists of groups of four ATB teeth followed by a single FT tooth. The convenience of needing only one blade for both common types of cuts can be a big selling point for many people. But remember that these blades won’t perform either type of cut quite as well as a blade designed for that purpose.
Triple Chip Grind (TCG)
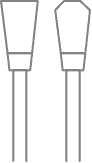
These blades alternate FT teeth with somewhat taller “raking” teeth having two beveled corners, so they resemble the top half of a stop sign. These sturdier teeth make them more durable than ATB blades. You’d use these blades to cut hard materials such as melamine, MDF, plastic, and laminates.
Number Of Teeth
The number of teeth on a blade affects both the smoothness of the cut and the speed at which you can feed material through the saw. More teeth means a smoother cut but requires you to feed the material at a slower rate. Blades with fewer teeth produce a rougher cut but let you feed the material faster. This added speed can be a big advantage when ripping many long lengths of wood.
In general, blades designed only for rip-cutting will have as few as 24 teeth. Cross-cut blades might have 60 to 100 teeth. General-purpose blades designed to handle both types of cuts often feature 40 to 50 teeth.
Hook Angle
A tooth’s hook angle, or rake, is its angle relative to a radius line coming straight out from the center of the blade.
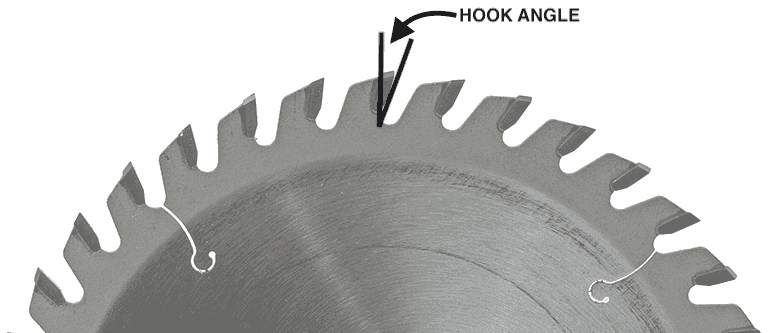
A positive angle indicates a tooth that angles forward, like a hook. The steeper the positive angle, the more aggressively the blade will bite into the wood. Rip-cut teeth often have high positive angles and general-purpose teeth more moderate angles.
Cross-cut teeth tend to have low positive angles or even negative angles. Negative angles make the teeth appear to lean backward. These teeth do not bite so aggressively into the workpiece, making for a cleaner cut.
Kerf Width
The kerf is the cut the blade makes as it removes material from the workpiece. A full-kerf blade has a kerf of about 1/8” (0.125”). A common mistake is forgetting to account for this 1/8” of lost material when setting up your cuts. So remember the famous adage—measure twice, cut once!
More powerful saw motors generally have no problem removing 1/8” at a time. Lower-powered motors (under 3 hp) might get bogged down, which can burn wood or stress your blade. To reduce the strain on these motors, you could consider thin-kerf blades, which usually have around a 3/32” kerf (though anything between .092” and .1” is common). Check your table saw’s manual for any restrictions on kerf width before purchasing new blades!
This difference may seem minor, but it means each cut is removing 25% less material. It also means you waste 1/32” less raw material with each cut, which appeals to some people. The dollar value of material saved isn’t likely to be significant unless you are working with exotic and expensive woods. Thinner blades are more prone to vibration and distortion, so look for models designed to reduce vibration.
Some manufacturers offer blades with ultra-thin kerfs as narrow as 1/16” (0.0625”), but these are specialty items that will probably require changing out equipment on your saw such as the riving knife. Look for full- or thin-kerf blades unless you have particularly extreme requirements.
Gullet
Each tooth has an empty space in front of it called the gullet. The gullet usually extends deeper into the body of the blade than the tooth itself does. This space allows the blade to remove wood chips and dust as the blade makes a cut in the workpiece.
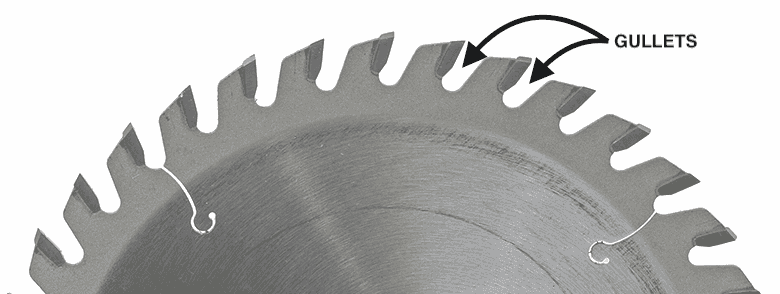
Cross-cut blades, with a large number of smaller teeth, have small gullets. A smaller gullet removes less material, meaning you must feed the piece more at a slower rate. Rip-cut blades have larger gullets to go with their larger teeth and faster feed rate.
Expansion Slots
The high speeds of a spinning blade generate friction that makes it very hot. Sometimes even dangerously hot to the touch. This heat also causes the blade to expand and contract, creating stress that can lead to warping. Thin slots allow expansion and contraction to occur without affecting the shape of the blade.
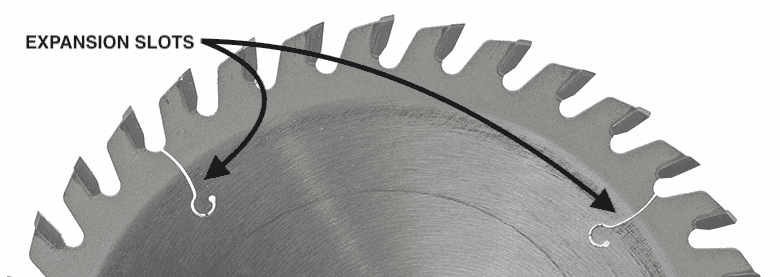
In the past, these slots went straight in from the outer edge, with a small circular bulb at the end to prevent stress fractures. Newer high-quality blades have very thin expansion slots laser-cut into the blade. This allows more complex curved shapes, sometimes in the body of the blade itself and not only at the edges. These thinner slots generate less noise than the old style. This might be worth considering if you want to reduce the noise from your saw—hard enough to do as it is!
Types of Materials and Cuts
Now we can look at the best choices for making different types of cuts in common materials.
Hardwood and Softwood Lumber
Boards made from solid hardwood or softwood have a grain—a specific orientation of fibers. Blades will behave very differently cutting with the grain or cutting across it.
Rip-cutting
Ripping wood refers to cutting lengthwise along the grain of the wood.
The right blade choice depends on whether you will rip your pieces to the exact size needed or if you’ll rip them a little bit larger and then trim them to size. If you can live with a rough first cut, a 24-tooth FT rip blade will make fast work of most types of wood. If you want a smooth cut on the first rip, without the need for more cleanup, opt for a 40-to-50-tooth ATB or ATBR blade.
The lower the tooth count, the faster you’ll be able to feed your workpiece through the blade. Never push the workpiece faster than the blade can handle when ripping. Doing so might bog down your saw or distort the blade.
Cross-cutting
Cutting across the fibers of the wood, called cross-cutting, takes much more work than ripping along them. For optimal cross-cuts you’ll want a blade with many more teeth than for ripping, so each tooth does less work. Having more teeth also leads to a smoother cut. The very smoothest results will come from an 80-to-100-tooth ATB cross-cut blade. For many purposes, though, you can get clean enough cuts from a 40-to-50-tooth ATB or ATBR blade.
General Purpose Cutting
You may notice 40-to-50-tooth ATB or ATBR blades mentioned in both sections above. They do a decent job at both rip-cuts and cross-cuts, though not as good as a blade designed for each specific job. Thus, you will often see these blades referred to as general purpose or all-purpose blades.
Don’t confuse the term “general purpose” with “combination blade”. The latter term refers specifically to an ATBR blade with two different types of teeth. Look beyond the “general purpose” moniker to see the exact tooth configuration. Then you’ll understand the strengths and weaknesses of that particular blade.
Sheet Goods
There are many varieties of sheet goods. We’ll discuss some of the common ones you’re likely to need to cut.
Plywood
Softwood or hardwood plywood does not have a specific grain direction. The grain alternates in each layer of wood, so there is no real difference in which direction you cut. The wood veneers are quite thin, so they are prone to tearing out if your blade makes too coarse a cut. A quality general-purpose blade, a 40-to-50-tooth ATB or ATBR blade, will usually suffice. If the plywood has an especially thin face veneer, switch to a higher tooth count such as an 80-tooth ATB blade.
Particleboard, Hardboard, Melamine, and MDF
These materials tend to wear out blade teeth due to their high density. Beveled teeth are especially prone to this. But a 40-to-80-tooth ATB blade will produce clean cuts if you can live with the wear. Switch to a TCG blade if the wear becomes too big a problem, although the cuts may not be quite as clean.
Plastic Laminate
Plastic laminate wears out blade teeth even faster than the materials above do. You can get away with using an ATB blade for occasional use. But plan on getting an 80-tooth TCG blade if you’ll need to cut a lot of laminate and don’t want to wear down your blade.
Metal
Normal table saw blades are generally not appropriate for sawing through anything but the very thinnest metal. You’ll want a more specialized blade, discussed below.
Special Features
Your project may have needs that go beyond the typical table saw blades discussed above. Let’s talk about a few less-common features that you might need to look for.
Diamond Coating
Aside from looking nice in jewelry, diamond is the hardest substance on earth. You may need its abrasive power for hard materials like composites, graphite, or cast iron.
Very finely-ground diamond makes up the working edge of diamond-coated blades. Don’t worry, this is synthetic diamond, not natural, so a blade won’t set you back as much as an engagement ring! These blades grind material away rather than cutting it, so they’re not useful for wood or other softer material. For that, you’ll need the cutting action of a regular blade.
Hardened Blades
You’ll want a special hardened blade if you need to cut through sheets of steel, copper, or aluminum. They may labeled for specific metals, or they might say they’re for “non-ferrous metals”. They are generally not appropriate for cutting wood or similar materials.
Be careful: When cutting metal with any saw, it’s important to avoid the risk of fire from sparks. Always make sure you completely remove all sawdust from the saw top and insides as well as from your work area.
Dado Sets
If your project requires you to cut a rectangular groove for a dado joint, a stacked dado set can make the job easier. It’s actually several blades attached to a single shaft called an arbor, so they rotate in unison. The outermost blades have a cross-cut configuration for a smooth cut on each side. The inner blades are flat to chip away the material in the middle. You can add or remove these inner blades as needed to make cuts of various widths. Some table saws, particularly portable contractor models, may not support using dado sets. Be sure to check your saw’s manual for details before buying this type of blade.
A related product called a wobble blade consists of a single blade mounted at an angle on a wide hub. The angle lets the blade cut away material all across its width. Wobble blades are often cheaper than a comparable stacked dado set. And since they are a single fixed piece that doesn’t need adjusting, they’re (in theory) easier to use. But they do suffer from a couple of drawbacks. The shape can cause significant vibrations that you may find difficult to work with. And they don’t make as clean a cut as a stacked dado set, so prefer to use the latter if possible.
Summary
If you’re only going to own one table saw blade, your best bet is a 40-to-50-tooth ATB or ATBR blade. Look for a blade marked “general purpose” or “all-purpose”. It’ll do a good job of cutting the materials you’re most likely to use: plywood and softwood/hardwood lumber. And it’ll make good enough rip-cuts and cross-cuts for most home improvement projects.
When you’re ready, consider adding two more blades: a 24-tooth FT blade for easy ripping and an 80-to-100-tooth ATB blade for clean cross-cuts. These blades will do a poor job at other types of cuts, so make sure you’re willing to take the time to swap them out as needed. If you don’t want to spend this extra time, you might be better off sticking to a single blade. (No judgment here! I’m pretty lazy and like to leave my general purpose blade installed all the time. For many of the projects I tackle, it does the job fine.)
Beyond these basic blades, let the needs of your projects dictate what other features you need in a blade. If you’re not sure you’ll need to use a specialty blade more than once, you might ask a friend to let you borrow theirs. Take the plunge and buy your own once you know you’ll use it.
No matter what, take sensible safety precautions and follow the operating instructions for both blade and saw!